There is a need for improving business results by increasing the quality of products, services and processes. The tools and techniques to achieve a greater level of quality in the past may not be good enough for today. The changing needs of society, customers, shareholders and regulators are some of the reasons why organisations must continually improve their quality levels. And, the person who has added the human dimension to quality - broadening it from its statistical origins is Dr J M Juran, more popularly called as the ‘father’ of quality. This article highlights Dr Juran’s key contributions in the field of quality management as the industry celebrates his 100th birthday on December 24, 2004.
Since quality cuts across all parts of the company and must be managed at every management level and by every worker, it is clear that quality is not just the function of the quality department. Quality is everybody’s responsibility, and everybody must be capable of doing this job. The consequences of this are enormous. Each person must be involved, trained in the basic quality methods, and clearly understand his or her part and how it affects the product, the service and the customer. However, different jobs have very different training needs. While there are common principles of quality management, there is no simple set of quality methods that apply universally to billing, design, research, manufacturing, sales and so on. Companies have to understand these different needs and train the employees for each job. At the same time, they have to create a common language, a common set of goals, and a common understanding of the customers’ needs.
The Indian corporate scenario
In view of the managerial complexity, and in order to gain a competitive position, Indian companies have more or less mounted on a massive quality-training programme. However, there is not a single organisation that overestimates the amount of training necessary to do this job, or over-invests in it. Companies lack in-house expertise on the basic elements of quality management, statistical methods, and teamwork that must be taught. They also lack the facilities, programmes and logistical support. Only a few like the Aditya Birla Group, Reliance Group, Larsen and Toubro, HDFC, Hindustan Lever and Tata Consultancy Services, are addressing this issue.
Objectives
There are several distinct objectives for this training. First, an awareness must be created throughout the organisation on the importance of quality, of the seriousness of the competitive challenge, and of the potential for breakthrough improvements. This basic knowledge and set of attributes must be held by everyone and understood at a level that will equip and motivate them for action. The goal, after all, is not that employees know about these ideas, but that they act on them. This is in reference to the intensity of knowledge sufficient to bring about basic changes in behaviour.
In the late 1980s, three corporate leaders - Chandra Mohan of Punjab Tractors, Dr B K Modi at Modi Xerox and R Srinivasan at lTC-Paper Products Division - did not delegate this responsibility, by choice. In doing so, they created a culture of continual improvement. The common vehicle these leaders adopted was ‘Juran on Quality Improvement’ video series. However, their training effort needs to be bench marked against that of Robert Galvin of Motorola and Jack Welch of General Electric, each of who realised breakthroughs or ten-fold improvements to face the competitive challenge.
The second objective relates to teaching specific technical concepts and tools. The exact needs vary with employee levels and functions. However, a common set of statistical and problem-solving techniques has emerged that is fundamental to actually achieving concrete quality improvement. Moreover, these tools for quality indicates that they are best learned through active involvement and practice. According to Dr J M Juran, “Education without action is easily forgotten; education with action is remembered”. Therefore, companies face the challenge of augmenting classroom instruction books, manuals and videos with an apprentice-like programme. But, are there enough “teachers” to go around? As a challenge to this view, one could ask whether industry should really have to invest in training engineers and managers on quality and statistical tools and techniques? Should this not be the responsibility of academia?
Only a statistically trained manager or engineer can effectively move a company towards its quality goals. The quantum of trained managers and engineers can benefit the market penetration efforts of companies. The American Society for Quality (ASQ) provides a good benchmark because it is perhaps the most focussed and recognised certification body for quality professionals in the English-speaking world. The ASQ conducts certification examinations twice a year, globally, for several specialisations like quality engineer, reliability engineer, quality improvement associate and so on. Each covers a defined body of knowledge that includes quantitative methods.
The third objective relates to teaching ‘managing for quality’. To do this, in addition to the technical tools of quality improvement, managers must learn a new quality management system. As a foundation, basic skills must be developed in The Juran Trilogy: quality planning, quality control and quality improvement. Each of these processes is carried out by a universal sequence of steps as summarised in the following quality map:
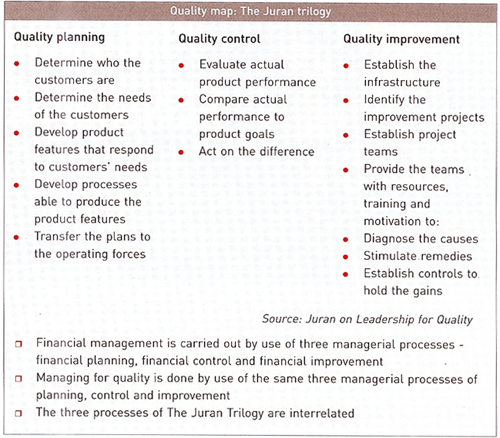
Key Benefits
Where should one start? Based on the experience with ‘Juran on Quality Improvement’ in India, it has been established that this is the most practical trilogy process to improve not only quality but also the bottom line for any organisation. The quality improvement process addresses chronic waste in an organisation. This chronic waste can be valued (cost of poor quality) at one-third of total costs.
If an organisation were to set a strategic goal to halve the cost of poor quality in two years, it could double its profits, with negligible investment. Examples abound of organisations in India that pursued this strategic goal (perhaps, over five years): Tata Steel, Mahindra & Mahindra (Tractor Division), Punjab Tractors, lTC-Paper Products Division, Cummins Engine, Bajaj Electricals, Crompton Greaves, Citibank, Jet Airways and so on.
And finally, there is a unique training requirement. A very key skill that must be learned by management and workers alike is teaming. Companies that have successfully implemented the quality revolution across the world have utilised the teaming process to a far greater extent than has been the tradition in industry in general. Teams are absolutely necessary to cut across organisational boundaries and attack the major quality problems. Thus, the psychological component of training is vital.
CREDITS: Suresh Lulla, Founder & Mentor, Qimpro Consultants Pvt. Ltd.