A total quality approach will be a prerequisite for the survival of most Indian companies by the year 2000 AD. Many companies will have reached levels of efficiency and quality unimagined till now. Others will be scrambling to keep up. Total quality will play a vital role in attaining leadership in the domestic and the international environment.
The total approach to managing for quality includes: quality planning, quality control and quality improvement and is commonly referred to as The Juran Trilogy (refer Exhibit 1). Indeed, all the three processes are important and are interrelated.
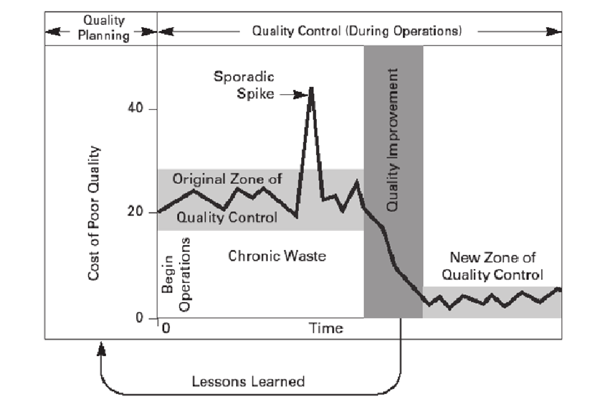
The Alligator Analogy
This interrelationship has been described by the plight of the fabled manager who was upto his waist with alligators (problems). Underlying this analogy, each live alligator is a potential quality improvement project. And each completed improvement project is a dead alligator. If our fabled manager succeeds in exterminating all the alligators, quality improvement would be complete - for the moment. However, the manager will not be finished with alligators because, there will always be new alligators. This is because the planning process remains unchanged.
In effect, the quality planning process is a dual hatchery. A benign hatchery produces new useful quality plans, while a malignant hatchery produces new alligators. Quality improvement can take care of existing alligators one by one. However, to stop the production of new alligators requires shutting down the malignant hatchery. This would help in curbing the problem at its very source. Companies should reexamine their approach to quality planning for the damage done by deficient quality planning has far reaching consequences.
It results in lack of competitiveness which translates into reduced sales and income. Another negative outcome is the cost of poor quality which will arise due to reworking.
Quality Planning
Quality planning is the activity of:
- Determining customer needs
- Developing the products and processes required to meet those needs.
An analysis of the traditional approach to quality planning reveals the following:
- Planning is done by experienced amateurs who lack adequate knowledge in the concepts, methods and tools of planning for quality
- Lack of participation and the use of “over-the-wall” approach to quality planning. That is, marketing hands the specifications of a product, to engineering which after completing the design throws it “over-the-wall” to manufacturing which is then responsible for putting the product together, and so on
- Use of empirical methods to test and optimize designs and processes
- Transfer to operations without proof of adequate process capability.
The use of the traditional approach to quality planning can have several detrimental effects:
- Unability of the product to satisfy customer needs
- High cost of design changes
- A longer time period between new product launchings
- Carry-over of defects from one design to the next.
To overcome such deficiencies, companies need to adopt modern method for quality planning. This modern method can be generalized into one coherent, universal series of input-output steps. Collectively these steps make up the quality planning roadmap. The steps on the quality planning roadmap are as follows:
- Identify who are the customers
- Determine the needs of those customers
- Translate those needs into our language
- Quantify the needs
- Develop a product which can respond to those needs
- Optimize the product features so as to meet our needs as well as customer’s needs
- Develop a process which is able to produce the product
- Optimize the process
- Prove that the process can produce the product under operating conditions
- Transfer the process to the operating forces.
A graphic representation is presented as Exhibit 2.
The above sequence is stitched together through several commonalities:
- The interlocking input-output chain, in which output for any step becomes the input for the next step
- The establishment of common units of measure for evaluating quality
- The triple role concept, under which every activity plays the triple role of customer, processor and supplier (refer Exhibit 3).
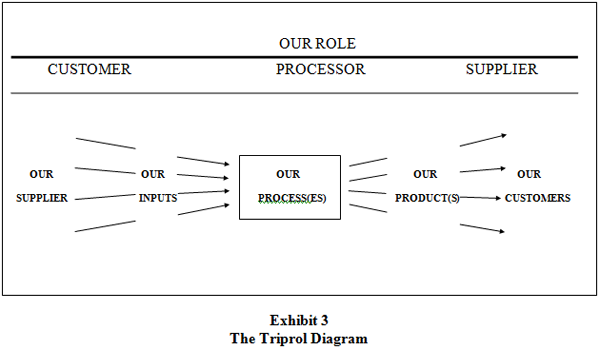
Who are the customers?
The first step in the universal sequence in quality planning is to identify who are the customers. A simple way of accomplishing this task would require a study of the existing product/process used to make a similar product.
The flow diagram is a planning tool widely used to help identify who are the customers. A flow diagram depicts the various steps in a process and their interrelation. A flow diagram provides a multidepartmental team of managers with:
- an understanding of the whole process
- helps identify opportunities for improvement
- helps identify customers previously neglected.
Keeping the Triprol concept in mind and keeping in mind that anyone impacted by the process is a customer, all customers need to be identified.
Customers are of various kinds:
- External: end user, wholesaler, customer
- Internal: various departments affected by the flow of product
- Hidden: government regulators, society at large.
Thus, customers are a cast of characters.
The next step in the planning process is the classification of the customers, according to the size of the impacts. The most common such classification is by the use of the Pareto principle. Under this principle, customers are classified into two basic categories:
- a relative few (vital few) who are of great importance
- a relative large number of customers each of who is only of modest importance (this “useful” many).
Exhibit 4 presents this relationship graphically. The vital few customers usually include amongst others, buyers of our products, government regulators, senior managers, whether internal or external, and labour union officials.
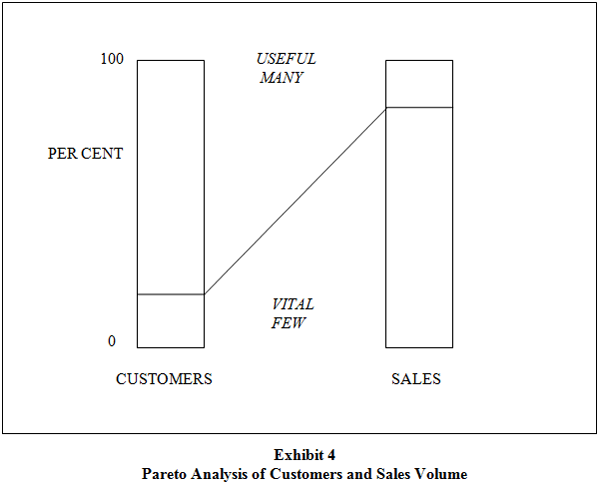
This step of identifying customers is a very important step in the planning process. Upper managers should assure that the methods in use for identifying customers are able to provide the quality planners with the essential customer base.
Customer’s needs
Discovery of customers’ needs is the second step on the quality planning roadmap. To identify customer needs, be a customer, communicate with customers or simulate customers’ use. Needs are of various kinds.
Stated Needs and Real Needs
Human beings need nourishment, shelter, transportation, etc. To meet these real needs, they buy food, dwellings, bicycles etc. Thus we need to secure answers to questions as:
- What benefit are you hoping to get from this product?
- What are the features which lead you to buy this product rather than a competing product?
Securing such answers usually requires a lot of hard work.
Perceived Needs
With growing affluence, customers’ needs proliferate into areas which can be baffling to technologists. Identical goods and services command radically different prices, depending on the shops in which they are sold - budgets, brand loyalties and mindsets to an extent which make the facts academic.
Cultural Needs
These abound. Among internal customers they relate to such needs as job security, self-respect, respect of others, and still other elements of what are broadly called cultural values. While such needs are real, they are seldom stated openly.
Needs Traceable to Unintended Use
Many quality failures arise because the customer uses the product in a manner different from that intended by the supplier. For example, the truck is overloaded, the tyres are underinflated, the oil is never changed, documents are misfiled. Planners should dig in and learn what will be the actual use (and misuse) and what are the associated costs. Acquiring such information obviously requires close teamwork between supplier and customer. Quality planning will be deficient if the knowledge of customers’ needs is deficient. The quality planners must accept the reality that in a competitive society the customers have the last word. The customers’ needs may be unstated, they may seem “unreal”. Yet the customers’ needs must be discovered, and they must be acted on.
Methods for Determining Customer Needs
There are several ways for determining customer needs:
- Be a customer
- Communicate with customers
- Market research
- Simulate customers’ use
It is important to note that customers’ needs do not remain static. There is no such thing as a permanent list of customers’ needs. Companies must continuously interact with potential customers through market research to update their list of customer needs.
Organizing the Information
An essential part of good quality planning is to use structure - to organize the information so that work is clearly defined, responsibility is established, etc. The needs of customers are so numerous that planners have evolved systematic approaches to deal with such large numbers. One such system is to organize customer needs into a logical interrelated pyramid of needs: primary, secondary, tertiary, etc.
The most convenient form of orderly arrangement is the spreadsheet (matrix, quality table, etc). In the spreadsheet, the customers’ needs are listed in the left hand column so that each row is devoted to a single need. Distinction among primary, secondary and tertiary needs (and so on) is made by differences in the amount of indentation from the left-hand margin. Exhibit 5 lists some customer needs for automotive travel. As seen in Exhibit 5, only the left hand columns of the spreadsheet have been filled in. The remaining columns will be filled in as the quality planning progresses. The columns will show such information as product features, unit of measure, goals, etc.
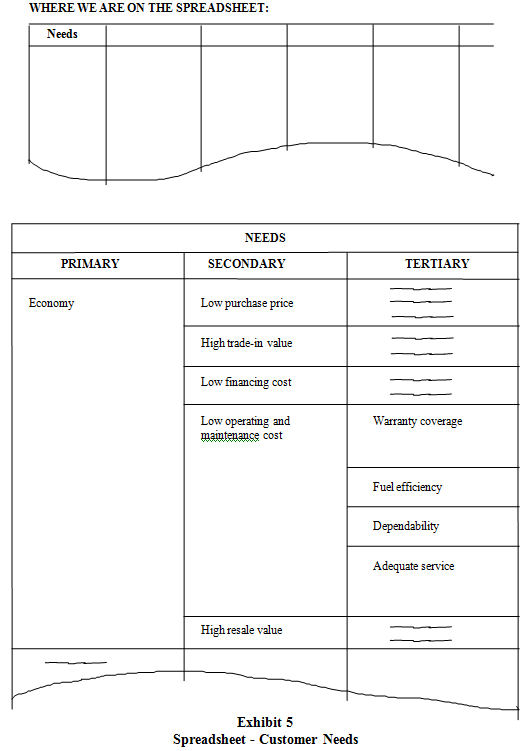
Translation
Customer needs may be stated in any of several languages:
- the customer’s language
- our language
- a common language.
When customer needs are stated in the customer’s language it becomes necessary to translate such needs into either our language or a common language. This necessity applies to internal customers as well as to external customers. Translation within and between companies is plagued by the limitations of language. Identical words have multiple meanings. To overcome such confusion requires agreeing on the precise meanings of key items and then publication takes the form of a glossary - a list of terms and these definitions. The publication may be embellished by other forms of communication sketches, photographs, videotapes.
The translations are entered into the vertical column adjacent to the list of customer needs (refer Exhibit 6).
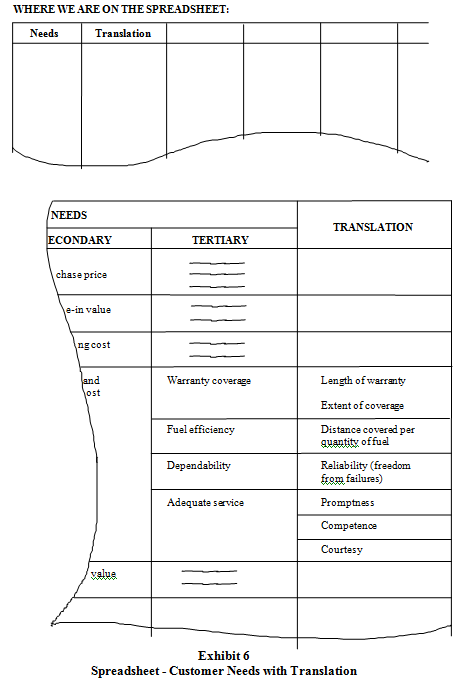
Product Development
Product development is the activity of determining the product features which respond to customer needs. Here, the word “product” is defined very broadly, so that the end result of product development can consist of designs, reports, specifications, computer programs etc. Also, it covers a variety of end results. The most important product is the goods and services which bring in the company’s income.
Every product feature should meet certain basic criteria of:
- Meeting the needs of our customers
- Meeting our needs
- Meeting competition
- Minimizing the combined cost of customer and supplier.
The product development function makes use of multiple disciplines for determining product features. In the case of goods, the major response to customer needs is through technology. Technology, while necessary, is no longer sufficient. Growing competition and society’s dependence on quality requires that the disciplines for determining the product features include quality-oriented disciplines. Some important ones include:
- Models and data systems for evaluating are predicting product reliability and maintainability
- Process capability studies for evaluating and predicting productivity
- Spreadsheets for assembling numerous interrelated data into condensed, easy-to-grasp forms
- Methods for evaluating the cost of poor quality.
These modern quality planning tools, have had limited use, so far, in industry. A major reason for their limited use is that in many companies, the product developers have lacked training in such tools. Senior managers in companies should take steps to assure that product developers are trained in the use of modern ways of quality planning for product development.
Product Design
Product design is the activity of defining the product features required to meet customer needs. Product design is a creative process based largely on technological or functional expertise. A good deal of product design is technological in nature but this technology interacts with the methods and tools of quality planning.
Product designs should be optimized to minimize the combined cost of user and supplier and meeting their joint needs. To overcome suboptimization within and external to the company, participation from various departments during quality planning is essential. This can be accomplished through design reviews or through joint planning. The benefits of participation are formidable and include:
- Early warning of upcoming problems
- Data to aid in finding an optimum
- Challenge to theories.
Creating such participation requires creation of an atmosphere of mutual trust to enable face-to-face meetings; sharing experience and feedback; exchange of critiques and ideas. The product features are listed in the vertical column in the spreadsheet. During the process of launching new products, use is made of three generic spreadsheets.
In the first of these spreadsheets the customer needs are listed in the horizontal rows. The vertical columns are then used to accumulate the product features required to meet those customer needs.
In the second generic spreadsheet the product features are moved into the horizontal rows. The vertical columns are then used to accumulate the process features required to produce the product features.
In the third generic spreadsheet the process features are moved into the horizontal rows. The vertical columns are then used to accumulate the process control features needed to keep the process at its planned level of operation (refer Exhibit 7).
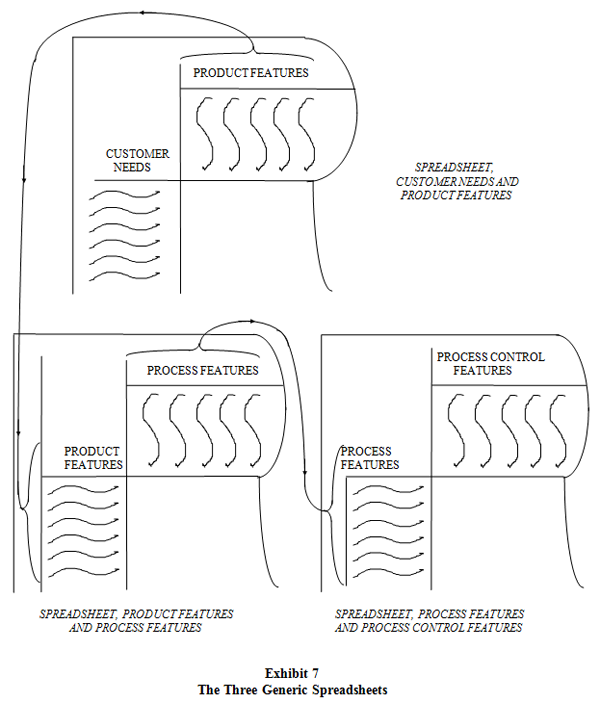
Spreadsheets aid designers in assembling a great deal of information into condensed, convenient form. However, spreadsheets do not provide answers; they are mostly a depository for answers which can require extensive data collection and analysis.
Although customer needs are usually stated in qualitative terms, resulting product features are expressed in quantitative terms. Exhibit 8 shows a list of customer needs and the corresponding product features.
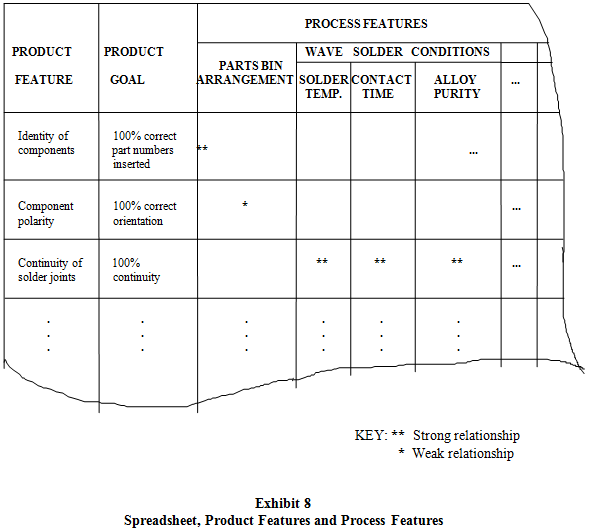
Once the product features are established, the next step is to set product goals. A goal is aimed at target. These goals then become the targets for the process developers and the operating forces.
Process Development
Process development starts with product quality goals and ends with a process capable of meeting the product quality goals under operating conditions.
Process development includes the activities of: product design review; choice of process; process design; provision of facilities; provision of software (methods, procedures, cautions).
Process design is the activity of defining the specific means to be used by the operating forces for meeting the product goals. This definition covers:
- the physical equipment to be provided
- the associated software
- information on how to operate, control and maintain the equipment.
An important aid to process development is an understanding of the predictability of process. Process capability studies help designers achieve this objective.
Process Capability
All processes have an inherent capability for performance. This capability can be evaluated through data collection and analysis. The resulting evaluation of capability becomes a valuable aid both during quality planning and during subsequent conduct of operations. This concept is applicable to manufacturing process and business processes; to manufacturing industries and service industries, to process run by the workforce process run by upper managers.
Process capability is an ancient and universal concept. What is new in recent years is to quantify process capability and to standardize methods, tools and terminology. Such qualification enables manufacturing planners to judge in advance whether specific manufacturing processes are able to hold proposed engineering tolerances.
In manufacturing processes, quantification of process capability has been quite extensive, and is based on evaluation of process variability. In quantified terms, process capability is equated to six standard deviations (six sigma) of process variability.
Although, extensive work is done to evaluate process capability, it is important to note process performance, which is the actual results achieved often falls short of the inherent variability.
The merits of process capability concept have led to the creation of data banks on process capability. Such data banks are used by planners in ways such as:
- Predict results in advance of conducting operations
- Secure early warning of deficiencies
- Choose the best from the available alternatives.
Data banks on process capability are found in all company functions and in the outside world as well.
Process Design
To arrive at an appropriate process design, planners need three key inputs:
- Knowledge of the product quality goals
- Knowledge of the product operating conditions
- Knowledge of the product capability of alternative process.
This requires process designers to be trained in the skills and tools associated within the planning process. This includes understanding of: the anatomy to capability; the nature and use of flow diagrams and spread sheets.
The next step is to optimize the process designs. The criteria for process design are similar to those for optimizing product designs - to meet the needs of both customer and supplier and to make the combined costs a minimum. As mentioned before, this can be accomplished through participation, design reviews and joint planning.
Exhibit 8 is an example of the process design spreadsheet, product features are listed in the horizontal rows. The vertical columns are used for entering various process features needed to produce the product features and meet the product goals. Process features include such things as processing equipment, instruments, process conditions etc.
The intersection of rows and columns are then coded to identify the areas and criticality of impact - which process features are pertinent to which product features.
Transfer to operations
This is the last step in the quality planning process. “Transfer to operations” includes a transfer of responsibility from the planners to the operating managers. However, prior to transfer, planners should prove that the process can produce the product under operating conditions to ensure better acceptability.
This can be accomplished in many ways:
- Proof of process capability
- The dry run under operating conditions. Any resulting product is not sent on to customers
- The pilot run
- Simulation studies
In some companies, transfer of the process from planning to operations is structured and formalized. Irrespective of the formality, an information package should be prepared consisting of standardized essentials: facilities to be used, procedures to be followed, instructions etc. Further, provision must be made for imparting any specialized training prior to transfer to operations. This is an important input which is often neglected.
Conclusion
The structured approach to quality planning has been used by a variety of manufacturing and service industries throughout the world. Their experience has been rewarding. Besides, many internal benefits of reduced time between new product launchings, fewer design changes, it has led to better customer satisfaction and increased market share. Companies need to be customer-driven for survival and this would require them to adopt the structured approach of quality planning to meet and satisfy the needs of their customers.
CREDITS: Suresh Lulla, Founder & Mentor, Qimpro Consultants Pvt. Ltd.