QCI’s national project on application of Lean Six Sigma tools in healthcare, conceived a year ago, has opened up new vistas to improve quality and productivity in healthcare delivery processes.
Lean Six Sigma (LSS) in Healthcare was conceived as a National Demonstration Project (NDP) by the Quality Council of India (QCI) approximately a year ago. This pioneering concept was the vision of Dr Girdhar J Gyani, Secretary General of QCI. Dr Gyani’s vision was to provide the NABH accredited hospitals in India, with a common platform for launching and managing their continuous improvement programmes.
The key objective visualised for the NDP was to achieve patient satisfaction and enhance the reputation of the hospitals.
Qimpro, a dedicated quality consultant for over 23 years, was appointed as the implementation partner for the NDP. Qimpro's role would include training and project facilitation.
Implementation Of the NDP
The implementation of the NDP on LSS in Healthcare was planned in two phases:
- LSS training for selected hospitals; and,
- Facilitation for identifying and executing LSS improvement projects in the selected hospitals.
From all the NABH accredited hospitals that had given their consent to be a part of the NDP on LSS in Healthcare, QCI shortlisted 10 hospitals in western and southern India. These hospitals include: P D Hinduja National Hospital and Medical Research Centre, Mumbai; Sterling Hospitals Limited, Ahmedabad; Godrej Memorial Hospital, Mumbai; L H Hiranandani Hospital, Mumbai; Narayana Hrudayalaya Hospitals, Bengaluru; Columbia Asia Hospitals Limited, Bengaluru; Amrita Institute of Medical Sciences, Kochi; Nethradhama Super Speciality Eye Hospital, Bengaluru; Manipal Hospital, Bengaluru; and G Kuppuswamy Naidu Memorial Hospital, Coimbatore.
The first phase of training on LSS was conducted by Qimpro consultants in two batches of three days each at Mumbai and Bengaluru, respectively, in January 2010. Both the training sessions were well attended with over 25 participants from the selected hospitals at each location. The participants received comprehensive material and training on the DMAIC phases of Six Sigma along with Lean Tools. After completion of training, a comprehensive plan was drawn up for facilitating the identification and execution of LSS improvement projects at each hospital over the next five months from March 2010 to July 2010. At least two projects were shortlisted for each hospital and a qualified Lean Six Sigma Black Belt from Qimpro was assigned to each hospital as a dedicated consultant. Each dedicated consultant made eight visits over five months to the assigned hospital to facilitate project teams through the DMAIC phase of Lean Six Sigma.
The projects identified at the various hospitals addressed a wide spectrum of chronic problems in the non-clinical processes that directly impact patient experience.
- Turn-Around Time for Patient Discharge
- Idle Waiting Time in OPD Services
- Turn-Around Time for Laboratory Reports
- Turn-Around Time for OT Services and OT Utilisation
- Turn-Around Time for Ambulatory Services
- Turn-Around Time for Comprehensive Health Checks
There was, however, one clinical project done by Nethradhama Super Speciality Eye Hospital on “Reducing the Average Residual Spherical Error” following Phaco emulsification with foldable Intra Ocular Lens Implantation for Cataract Surgery.
Throughout the NDP journey and during all the facilitation visits by consultants from Qimpro, there was total commitment and 100 per cent participation from all team members at the various hospitals. This helped the team members from various departments to sensitise to each other’s needs and created a cohesive bond among them. This also facilitated collaborative effort among the team members to solve an organisational problem with a positive approach without blaming each other.
The enthusiasm and energy with which the team members executed each project and attacked the problems identified, ensured that each project delivered significant positive results in improving the efficiencies of the non-clinical processes at each hospital.
The key drivers for all the positive changes are listed below for each identified problem area:
- Turn-Around Time/or Patient Discharge:
Turn-Around Time (TAT) for Patient Discharge was the most popular problem in the NDP and as many as six hospitals had identified it as a project. The key drivers for this change were:
- Challenging the mindset against preparing discharge summary on the previous evening.
- Collaborative ownership between nursing and doctors for minimising the time taken to check and approve discharge summary.
- Collaborative ownership between nursing and accounts for minimising the time taken to prepare the final bill and intimate the same to the patient’s relative.
- Idle Waiting Time in OPD Services
Idle waiting time in OPD was also a popular project in the NDP and the key drivers for reducing it were:
- Streamlining the appointment process and encouraging more appointment patients.
- Improving the patient flow between the various laboratories through better coordination.
- Advance intimation to patients with special needs before they came for the appointment.
- Turn-Around Time for Laboratory Reports
Many of the hospitals opted for improving this process. The key drivers for reducing the TAT for Lab reports were:
- Reducing waste of maintaining multiple entries for the same patient in multiple registers.
- Making radiologists accountable for releasing reports after a fixed no. of images were completed.
This also included a structured escalation process if reports were not released on time.
- Turn-Around Time for OT Services and OT Utilisation
- The main driver for change in this process was the reduction in the pre-surgery and post-surgery cycle times.
- Reduction in pre-surgery cycle time was achieved by pre-ponement of all activities related to surgical consents and financial approval to the previous evening.
- Reduction in post-surgery cycle time was achieved by improving the efficiency of clearing the OT after completion of surgery.
- Turn-Around Time (TAT) for Ambulatory Services
- The key driver for reduction in TAT for Ambulatory Services was extensive training and sensitisation of the nursing and ambulatory staff regarding the criticality of their process.
- Also mock drills were conducted by senior staff to demonstrate that shorter TAT was possible.
- Turn-Around Time (TAT) for Comprehensive Health Checks
- The key driver for reducing the TAT for Health Check process was the realignment of patient movement between the various test centers that best suited the layout of the hospital.
- A printout of the layout along with the patient’s route during the health check was handed over to the patient. This helped drastically reduce unnecessary idle time lost in searching the next test centre.
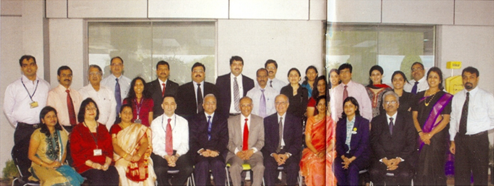
NDP Review
- The first NDP Review was conducted on May 18, 2010 at PD Hinduja Hospital in Mumbai and the Final NDP Review was conducted on August 11, 2010 at Columbia Asia Hospital in Bengaluru. Both the reviews were attended by over 50 participants from all the hospitals.
- Both the reviews were graced by Dr Gyani and Mr Avik Mitra from QCI along with Mr Suresh Lulla from Qimpro Consultants.
- Each project was scored by Dr Gyani and Mr Suresh Lulla on the following parameters:
- Introduction
- Quality of visuals
- Presentation skills
- Content
- Ability to field questions
- Time management
- The top three scorers were awarded with mementos by Dr Gyani and Mr Lulla as a token of appreciation. All participants of the NDP received Lean Six Sigma Green Belt Certificates.
- The high energy levels and total participation from all the team members were appreciated by Dr Gyani, Mr Mitra and Mr Lulla. They expressed satisfaction with the successful manner in which the NDP on LSS in Healthcare had been facilitated.
KEY SUCCESS FACTORS
- The top management at the various hospitals had personally been involved in implementing the improvements from these projects.
- This led to the team members taking ownership of the projects and has created an understanding that while the consultants were there to facilitate, they had to take ownership of implementing the change. This facilitated the easy understanding of the Lean DMAIC methodology and created a belief in the team members that they could equally participate in the execution of the project and not merely take instructions from the consultant.
- The problem areas identified for the projects were the most obvious pain areas and there was a need for practical solutions as the staff faced patient dissatisfaction in these areas every day. Hence solving these problems was an absolute priority for the team members.
- The structure of the DMAIC methodology has generated significant positive interest among the team members and they could visualise the distinct possibility of a practical solution at the end of the project.
- The team work promoted through process mapping, brainstorming sessions and data collection created a collaborative team and the team members appreciated new feeling of togetherness. They commented saying that this was the first time they had actually stepped out of their silos and practically “seen” the complete end-to-end process.
CREDITS: Quality Council of India