The Process Management Criterion of The IMC Ramakrishna Bajaj National Quality Award looks at a company’s operating systems - specifically the processes directly involved in producing and delivering the goods and services that have been selected through the organisation’s strategy formulation as outlined in the criterion ‘strategic planning’ (See Indian Management, August 2002). Process management considers how the processes that contribute to the production of the organisation’s wares are managed and improved.
The major questions in this criterion are:
- How are manufacturing or service-delivery processes controlled?
- How are products and services designed to meet customer requirements?
- How is the quality of systems, products and services assessed and improved?
- How is the quality of business processes, support services, and suppliers ensured?
Companies that score well in this criterion are strong in “process thinking”. They have evolved beyond managing products or departments in isolation to managing the processes that combine activities across departments. Customers, suppliers, and the company are brought together in common alignment. High-scoring companies develop comprehensive sets of measures to continually monitor the quality of their process. They regularly evaluate the “fitness for use” of all their processes, practices, products and services with the never -ending, single-minded purpose of improvement.
The quality of support services, business processes, the new products/services development cycle, and supplier quality are all ensured, assessed and improved.
In contrast, companies that perform poorly in this criterion spend most of their time correcting mistakes rather than preventing them. Interfunctional cooperation is low; product/service concepts are “thrown over the wall” from marketing or the senior executives, first to engineering and then to manufacturing. Control and assessment processes are loosely regulated. There are no evaluation change cycles; communication with support functions and suppliers is minimal.
Process management is primarily about the prevention of errors. It provides a foundation for building quality into production by eliminating errors at source. This is a major criterion, covering a great deal of ground. It starts with the conversion of customer requirements into design features and then winds its way through process-quality assessment and control, and the quality of support services and suppliers.
Naturally, there are many stops along the way to check for continuous improvement.
The principles, tools and techniques for process control can be found in almost any quality control handbook. For many processes, these techniques are quite straightforward and obvious. However, in the case of complex services such as education, healthcare and consulting, whose services are often more complex and often less amenable to quantitative analysis (and benchmarking) than are manufacturing processes, the path to control becomes less distinct.
Why this disparity?
Manufacturing processes are often more measurable. Interaction with customers is a much more predictable affair. The transformation of raw materials is sequential and routinised. In services such as consulting, by contrast, processes constantly fluctuate in response to new information. Five bad parts per million in the manufacture of screws is a nice, neat concept. But how do you define five bad parts per million in advertising, insurance or banking? Nevertheless, it is possible to set up tolerance variables against which to measure the acceptability and quality of a service, even if such measurement is based only on the subjective perceptions of customers (such as customer satisfaction and dissatisfaction)
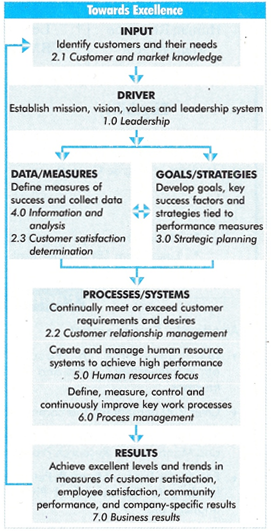
2002 IMC RAMKRISHNA BAJAJ NATIONAL QUALITY AWARD CRITERIA
CRITERION 6. PROCESS MANAGEMENT (140 POINTS)
The process management criterion examines key aspects of process management, including customer-focused design, product and service delivery, support services and supply management involving all work units, including research and development. The criterion examines how key processes are effectively designed, implemented, managed and improved to achieve higher performance.
Criterion parts: Evidence is needed of management of product and service processes (60 points), management of support processes (40 points), and management of supplier performance (40 points).
6.1 MANAGEMENT OF PRODUCT AND SERVICE PROCESSES
Describe how products and services are designed, implemented, and improved. Describe also how production/delivery processes are designed, implemented, managed and improved.
Suggested areas to address include how
- data on customer requirements are gathered
- designs are coordinated to include production phases, delivery
- customer requirements have been translated into engineering specifications and characteristics during the design phase of the new product development cycle
- customer requirements have been translated into service characteristics and standards during the design phase of the new service development cycle
- all appropriate personnel are involved in early stages of the design process - when their input has the most value
6.2 MANAGEMENT OF SUPPORT PROCESSES
Describe how the company’s key support processes are designed, implemented, managed, and improved.
Suggested areas to address include how:
- a systematic process has been defined for taking customer requirements and using them to design new/enhanced products and services in support functions
- standards have been set for each measure based on customer requirements
- procedures and mechanisms are in place to control key variables associated with quality
- in-process as well as output measures are used to assess quality in support departments
- measures of product/service quality in support functions are fed back to appropriate personnel who are empowered to make any necessary changes to improve performance
6.3 MANAGEMENT OF SUPPLIER PERFORMANCE
Describe how the company assures the materials, components, and services furnished by other businesses meet the company’s performance requirements. Describe also the company’s actions and plans to improve supplier relationships and performance.
Suggested areas to address include how:
- critical suppliers are identified
- measurable quality indices and requirements/standards have been identified for suppliers, and for what percentage of suppliers
- key suppliers receive regular feedback on performance on key quality indicators
- objectivity and reliability of measures of supplier performance are assured
- supplier processes, products and services are periodically audited and assessed
CREDITS: Suresh Lulla, Founder & Mentor, Qimpro Consultants Pvt. Ltd.