In 2006 I co-authored a paper titled ‘An ISO 9001:2000-based framework for realizing quality in small businesses.[1]’ In this paper we proposed a framework for an effective and efficient design and implementation of the ISO 9001 Quality Management System (QMS) standard, especially in small businesses.
- The recommended framework rests on four somewhat unusual and controversial premises to ensure success:
- rely on own people to develop the QMS.
- give the system and people time to settle.
- assign top operational manager to be the quality representative.
- do not seek certification.
The following table compares the traditional and recommended frameworks for ISO 9001 realization.
Recommended | Traditional |
1 | Real motive is quality | Real motive is certificate |
2 | Internal team develops QMS | External consultant develops QMS |
3 | Flexible project schedule | Strict project schedule |
4 | A top manager is mgt. representative | A designated person is mgt. representative |
5 | Certification is an option | Certification is a must |
Today, after 8 years, I have a firmer belief that the recommended ISO 9001 realization framework is the most rewarding and quality assuring one; even for large organizations. Stories of ISO certified organizations not realizing quality and business gains abound. The paradox is that these organizations are ‘successful’ in maintaining certification.
Traditional Framework
The following block diagram depicts the traditional framework for realizing ISO 9001. External consultants typically set the duration of the project at about 6 to 9 months. For competitiveness and financial reasons, it is unlikely to set it longer than 9 months; and in certain instances of ‘horror’ stories it took 2 to 3 months!
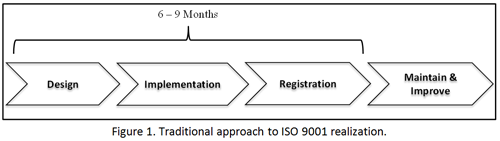
Recommended Framework
The recommended framework is incremental; it consists of three stages as follows (Figure 2)1:
- Single-process QMS; where the organization focuses on a single key business process that generates highest revenue/profit, has highest transaction rate, and/or consumes great resources. This allows the internal team to take the time to focus its effort and time, and ensure that real business gains are realized before commencing to the next stage.
- Basic QMS; where a simple QMS is developed around the single process by developing the six system processes required by ISO 9001; namely, records keeping, document control, preventive action, corrective action, control of nonconforming product, and internal audit. Again, the internal team takes the time and effort to ensure the system is stable before embarking on the final stage.
- Complete QMS; where the Basic QMS is expanded through fulfilling all remaining ISO 9001 requirements. Note that stage 2 and 3 are interchangeable; and organization may wish to expand to include all other processes before addressing the system processes.
As shown in Figure (2), the possibility of automation should be explored in all three stages. Automation may be useful in two ways; first, it may enable the key business processes through workflow automation, and second, it may assist with the administering of the QMS.
By using the recommended framework, the time of each stage is determined based on objective assessment of the degree to which each stage has achieved its objectives, and most importantly the achievement of the desired outcome; i.e. quality.
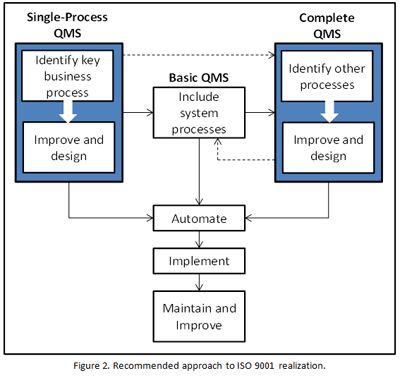
The decision on whether to adopt the traditional or recommended approach boils down to the top management real objective: Quality or Certificate!
Dr. Tariq A. Aldowaisan
Associate Professor, Kuwait University
Founding Partner & Senior Consultant, Gulf Lead Consultants
CREDITS: Dr. Tariq A. Aldowaisan