TQM system: Quality is now part of the executive vocabulary in India. For some companies, quality has become an important management issue focusing on ISO 9000 certification. These quality systems are a basic requirement. A handful of mature organizations have gone further. They have even realized that their long-term survival primarily depends on providing high quality goods and services, competitively. This has led these companies to embark on Total Quality Management (TQM) efforts, and means that quality is now being placed at the top of their management agenda.
One of the major elements of a TQM system is quality improvement. This is the organized systematic elimination of deficiencies, such as product scrap or rework, customer complaints, and material shortages. Usually, managers assume that everyone understands how to solve these problems, and that they can be solved without management organization and prioritization. The result is that symptoms of problems get treated. Remedial action on the causes is absent. The cornerstone of any successful TQM system is the organized elimination of waste, using structured quality improvement processes.
The other major element of a TQM system is a constant focus on the customer, in all forms of the company/customer transactions. This customer data is then tracked into the relevant company activities that support the design and delivery of products and services. Consequently, customer driven goals are an integral element of the quality planning process.
Inter-connected Processes
What becomes apparent to many companies over time is that the company is really a set of inter-connected processes - sets of tasks that go together to create desired outcomes. This may seem obvious on the surface, but the concept has significant implications. When we take a process view of the company, the following becomes apparent:
- Lack of common understanding
Whilst in principle everyone may understand that the company is a set of processes, no individual completely understands any one complete process. Putting different functional groups in a room to map out a process always produces shocks when the reality of how things get done is understood. A popular quality tool in this context is flowcharting. Examples abound of its exploitation in the electronics, textiles and engineering industries in India. - Lack of management ownership
No individual is responsible for the complete process, although each function has its own piece to manage for its own purposes. This leads to coping - departmental fixes or ‘band aids’ that everyone knows do not resolve the real problem. Major corporate processes tend to grow in an unplanned way over a number of years. We see ample evidence in our public sector and large private sector organizations. - Lack of measurement
Functional managers are measured, whether by budget performance, sales quotas or schedule performance. Each year, managers get their individual annual tasks which somehow they are expected to achieve. The processes carry on regardless, unmeasured. This is an axiom, countrywide. - Limitations of quality improvement
Organized problem solving has its limitations. There comes a point when improvement teams recognize that the process they are examining is either inherently unsuitable to the task or uncompetitive. Often, teams find that they cannot improve the current process sufficiently. What is basically needed is a plan for a different process. Hence, back to quality replanning - customer driven. - Sub-optimization
Sub-optimization is rife in many processes - by this I mean the pursuit and attainment of functional goals at the expenses of the process performance. In my personal opinion, this is the area that should obsess our upper managers.
BPQM
Many corporations in the USA have recognized these issues and added armoury to their Business Process Quality Management (BPQM). They include IBM, Ford Motor, NCR, Texas Instruments and AT&T. While implementation and terminology may vary, all these companies are addressing the same issues in similar ways, and in many cases results have been truly remarkable in terms of both effectiveness and efficiency.
Each of them concluded that its basic processes had become like hardened arteries - the blood was pumping, but it wasn’t moving easily. The result was that processes were poorly understood, inefficient and ineffective, and full of redundancies and rework. As the processes deteriorated over time, each function added to its own checking and rework to protect itself, and overall performance spiralled downwards.
They eventually decided to develop BPQM methods to ensure that:
Improvement projects can lead to major process change
- Key processes are documented and measured
- Process measures are used as management decision-making aids
- Process designs are competitive
- Processes are constantly reviewed
- Ownership exists to ensure continuous improvement
- Functional boundaries are not hindrances to performing key business tasks
- Current practices and thinking are challenged via benchmarking world leaders
In short, they wanted key processes managed year over year to achieve best-in-industry or world class status. The lessons learned should serve as a basis for improving Indian competitiveness, in leaps, at a revolutionary rate.
It is with regret that I find myself unable to illustrate this article with examples drawn from Indian industry. The reason is that no one yet has taken this opportunity to leapfrog the early stages of quality consciousness and involvement to the actual application of Total Quality Management.
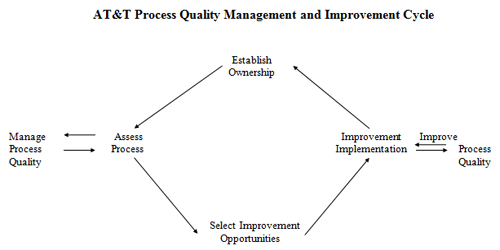
CREDITS: Suresh Lulla, Founder & Mentor, Qimpro Consultants Pvt. Ltd.