World class companies demonstrate a sharp customer focus. This focus is based on the belief that the customer defines quality; the customer is the final inspector; the customer pays one’s salary. All this seems very obvious. What is not very obvious is how to respond to changing customer needs, efficiently and effectively.
Managing for Quality
Defining quality is as complex as defining "peace". When asked to define quality one gets a flood of authoritative definitions. Most definitions are singular, such as, conformance to specifications, zero defects, customer satisfaction, best-in-class, fitness for use, and so on. On structuring these definitions one discovers that, in reality, quality has dual meanings:
- Product features that satisfy customer needs
- Freedom from deficiencies that reduce customer dissatisfaction.
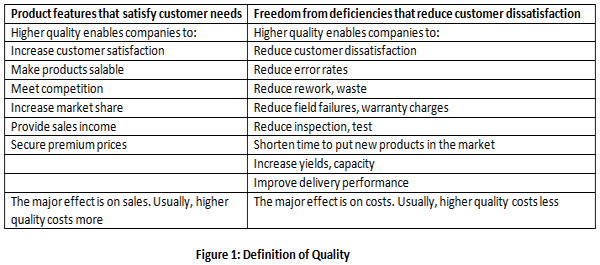
The goal of any customer focused organization is to offer product features that satisfy customer needs better than competition can, and to completely eliminate the opportunities for deficiencies within and without the operations. The former addresses effectiveness, while the latter addresses efficiency. In other words, there is no room for error, whatsoever. Ultimately, one’s ability to delight the customer, effectively and efficiently, has a direct bearing on the product life cycle.
As articulated by Dr J M Juran, managing for quality uses the same three processes needed to manage for finance. To manage for finance we work with financial planning, financial control and financial improvement. Similarly, to manage for quality, we require quality planning, quality control and quality improvement.
The output of financial planning is the budget. A budget has an annual frequency, and involves top-down and bottom-up participation. However, the ultimate accountability for a budget is squarely anchored at the top of the pyramid. As is known, responsibility for a budget is not fully delegable, by upper management.
Quality planning has no shadows of PERT and CPM. Quality planning starts with identifying customers and ends with proving process capability (refer figure 2). In other words, process capability is to quality planning what budget is to financial planning. With a poorly defined budget, one cannot be certain of planned profits. Likewise, with an incapable process, one cannot be certain of quality. Leadership for quality planning must enjoy the same stature as that for financial planning. Consequently, the responsibility for defining process capability is not fully delegable.
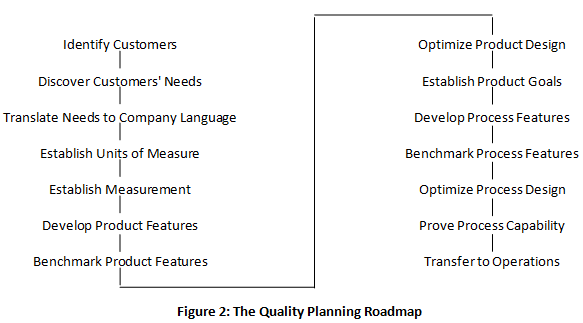
Since customers and their needs can be assessed by competitors also, the goal for any organization should be to satisfy the customers’ needs faster, better and cheaper than competition. This clearly requires fine tuned quality planning. There is no better advantage than being first in the marketplace.....prior franchise. The business benefits that accrue are in terms of premium prices and market share. All this necessitates a proactive paradigm to get the customer to vote for one’s product with his/her money.
Quality control is to quality management what financial control is to financial management. A control process, by definition, compares actual performance against the target, computes the difference and takes managerial action on the difference. In financial management, this is referred to as cost control. In quality management, the same is referred to as quality control. The frequency for control may vary from a minute to a month. The responsibility for control is substantially delegable.
In the control feedback loop (refer figure 3), the flow of events progresses as follows:
- The sensor which is plugged into the process, evaluates actual performance
- The sensor reports this performance to an umpire
- The umpire also receives information on what the goal or standard is
- The umpire compares actual performance to the goal. If the difference warrants action the umpire energizes an actuator
- The actuator makes the changes needed to bring performance into line with goals.
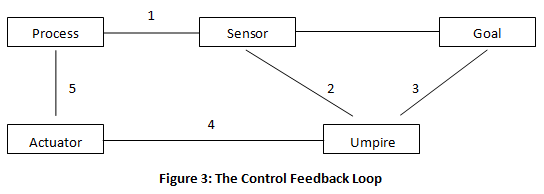
To conform to specifications, all the vital processes must be well documented prior to transfer to operations. Management through ISO 9000 quality systems is sufficient. The accent of the ISO 9000 system is on conforming to specifications, delivering the product by the contracted time and keeping costs under check. This requires companywide participation. It is particularly useful when one is expanding the volume of business.
As a strategy, quality control is only as good as the standards set to satisfy customer needs. Customers are known to change their minds based on the ability of new competition to nullify one's strengths. As customers change their minds, the response should be by reviewing and updating the existing standards.
Quality improvement is to quality management what financial improvement is to financial management. One should improve one's products and processes incrementally and continuously at a rate faster than the defined competition. Apart from reducing the chronic waste in processes, improvement must focus on eliminating customer dissatisfaction. Collectively, all improvement can save costs associated with waste, warranty and cycle time.
Since the objective of competition is to nullify one's strengths, the proactive focus should be on improving strengths. Improving strengths is inevitable. If improvement of one's strengths is a reaction to competition, quality and market leadership could be lost. Hence, to retain leadership, continuous improvement upon one's strengths, is mandated.
The quality improvement process is the means of raising quality performance to unprecedented levels (breakthroughs). The methodology consists of a series of universal steps as presented in figure 4. These steps have been tested and proved in the Indian environment.
Dependence only on the ISO 9000 quality system may offer disappointing results. In a competitive environment, the strategy should be continuous quality improvement as an integral part of a quality system. In fact, American auto manufacturers, worldwide, have adopted an updated system to address precisely this issue: QS 9000. Vendors to American auto manufacturers, in India, are required to install a QS 9000 quality system to qualify as preferred suppliers. Other industries should take a cue from this approach.
The three quality management processes namely, quality planning, quality control, quality improvement are referred to as The Juran Trilogy. They are interrelated (refer figure 5) and applicable to all products, industries and functions.
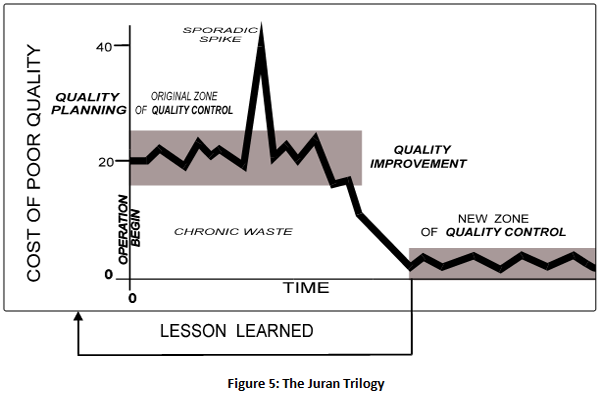
Product Life Cycle
With the opening up of the Indian economy, multinational companies have demonstrated that growth industries have been heavily built on new products: auto, auto ancillary, software, readymade garments, processed foods, and so on. This factor will assume even greater importance in the future as competition continues to intensify and the flood of new products crash the life span of existing products.
New products have a characteristic pattern to their sales-volume and profit-margin curves (refer figure 6). While these two curves are similar in configuration, the profit curve tends to start descending while the sales curve is still rising. A total approach requires monitoring both curves.
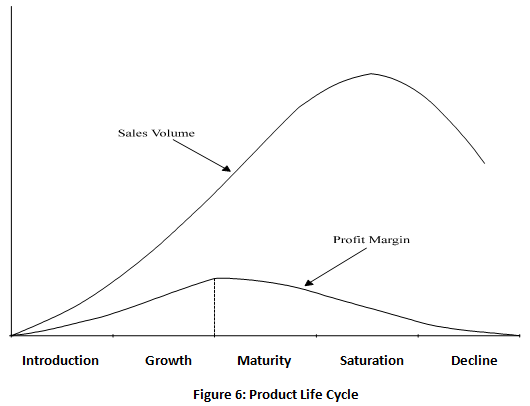
In a protected economy, the sales curve was adequate as a basis of planning for marketing strategy. Now, realizing the out-of-phase relationship between the profit curve and the sales curve, managers understand that product strategy is better planned around the profit curve than the sales curve. As a planning tool, this is easier to recommend than implement. Unless, on the other hand, a company is also adept at managing for quality.
A primary economic conclusion, derived from analyzing the life cycles of numerous American products, is that sooner or later every product is preempted by another or else degenerates into profitless price competition. This inevitable fact makes clear the necessity of careful new-product planning to maintain profit margins.
The sales-volume and profit-margin patterns, as well as, the timing of the product life cycle vary by product and industry. As a generality, the closer the company is to consumer goods and the market place, the shorter the cycle of its product. Conversely, the closer the product or the company is to basic industry or producers' goods, the longer the cycle. The position that a particular company has in the spectrum from consumer goods to basic goods
may well dictate the amount of money, time and management accorded to the new product activity. However, it is clear that the time scale on almost all products is continuously being shortened by accelerating research and technology and changing markets, mass media and mass distribution.
Synergistic Advantage
We have dwelt on two concepts so far: managing for quality and product life cycle. The objective of this section of the paper is to examine the synergistic advantage of integrating the two concepts. The objective being to bring health to the profit margin.
In the introduction phase, the strategy of management should primarily revolve around reducing the cycle time to introduce a product. This can best be achieved by exploiting the quality planning process. The relevant advantages of quality planning during this phase are:
- Product goals have been established after addressing customers' needs, benchmarking product features and optimizing costs
- Process goals are established after addressing product goals, benchmarking process features and optimizing costs
- Operations commence only after establishing process capability.
While all this additional planning appears to be much effort, the overall time for introduction is reduced because of lesser mistakes during launch. This provides a clear competitive advantage in terms of being first in the market place (refer figure 7).
During the growth phase, it is critical that the product is consistent in terms of the claimed features and performance and the actual features and performance. To nurture consistency, management must use the quality control process. In its current incarnation, the process is better recognized through the ISO 9000 system.
CREDITS: Suresh Lulla, Founder & Mentor, Qimpro Consultants Pvt. Ltd.