Introduction
A battery cell is usually available in four distinct sizes throughout the world. The variety of sizes should fit all equipment that require cells to operate. A company that produces cells that deviate from these standard sizes will probably find no takers (buyers) and would find itself out of business, no matter how good the quality is. But are standards a guarantee for quality? Certainly not. Standards are important and were developed to achieve amongst others, uniformity, intercommunication and interchangeability.
Quality standards are documents that define the contractual, functional, and technical requirements for all quality activities that will ensure that a product, a process, a service or a system is fit for its intended purpose. The achievement of such standards should be seen as the minimum requirement to be successful. In fact, to achieve world class quality, it is necessary to go beyond the standards and look at continuous quality improvement and customer satisfaction.
History
The quest for quality and uniformity in items such as pottery, footwear, armour and ornaments led to the use of physical samples as standards. The masters of workshops would visit the craftsmen frequently to see that work produced was “good”; however this judgement was based on knowledge, experience or often just the item’s appearance creating uncertainty of acceptance to the craftsmen.
Written standards were first developed in the early years of this century. Large groups such as the defence organizations of Great Britain and America wrote standards for their ordinance products to ensure product interchangeability, to reduce manufacturing costs and to reduce inventories. Soon after World War II a large number of product standards became available. The standards writing process varied from country to country. In order to get some order and a uniformity of language, the International Standardization Organization (ISO) took upon the task to write a generic quality standard. ISO, the specialized international agency for standardization is headquartered in Geneva, Switzerland and is made up of national standard bodies of 91 countries, India being one of them. ISO developed the ISO 9000 series in 1987 and this standard has gained unanimous acceptance worldwide as a quality system standard (see annexure 1). In India, the IS 10201 Parts 2-6 series is exactly the same as the ISO 9000 : 1987.
ISO 9000 Series
Definition
There are five standards in the ISO 9000 series. The ISO 9000 standard provides some basic definitions and concepts and summarizes how to select and use other standards in the series.
The ISO 9001, 9002 and 9003 standards are applicable for external quality assurance purposes for contractual situations. ISO 9001 is to be used to ensure conformance to specified requirements during design and development, production, installation and servicing. ISO 9002 is used when only production and installation conformance are to be ensured. ISO 9003 is the least detailed standard and requires only that conformance in final test and inspection be ensured.
ISO 9004 contains guidance on the technical, administrative and human factors affecting the quality of products and services. This standard is for internal use only and is not to be used in contractual situations. The standards list the essential elements that make up a quality system in some detail, starting with the responsibilities of management. Whole sections are devoted to each aspect of the quality system: marketing, design, procurement, production, measurement, post production, materials control, documentation, safety and the use of statistical methods. This standard could be used to evaluate a company’s progress towards a fully implemented quality system. This is where a company should begin their implementation of the ISO standard.
Exports
It is perceived that ISO 9000 accreditation will be a requirement to do business with Europe after 1992. However, it is not a requirement unless the buyer company emphasizes it. The wider acceptability of the ISO 9000 in Europe and other parts of the world will make registration to the ISO 9000 a compulsory requirement for exporting to these countries. But, supplier surveillance will not be eliminated because manufacturers have special requirements not specifically called for by a general application of the standards.
Benefits
There are several benefits of registration including:
- It is one standard that has almost universal acceptance
- Fewer, more focused supplier audits
- Easier, faster and more comprehensive learning
- Increased productivity and quality caused by better systems
- Sales in the European community
- A recognizable logo that can be added to sales literature
- Being listed with registered suppliers in a registry.
But there are certain shortcomings that companies need to be made aware of:
- These standards are generic. They represent the minimum requirements for an effective quality system to assure that the product will meet customer requirements. These standards define what must be in a quality system but do not tell a company how to document the quality system. What is a quality manual? What makes up an adequate quality plan? What makes up an adequate quality policy? These questions are not answered.
- These standards do not make provision for continuous improvement. This is a serious drawback that, perhaps, will be addressed in the future. Until then, continuous improvement to lower costs, to improve product and service quality, and remain competitive in today’s world economy is still the responsibility of management.
- The ISO 9000 series requires no evidence of a satisfactory track record of performance, eg. in product quality or delivery.
Beyond Standards
To achieve world class quality, it is necessary to look beyond the ISO 9000 standard and institute continuous quality improvement within a company as well as to provide goods and services that satisfy customer needs.
Continuous Quality Improvement
A good way to institute continuous quality improvement is to use a structured approach based on the project-by-project breakthrough process developed by Dr J M Juran. Experience has shown that such breakthroughs in performance require a series of contributing breakthroughs. First, there must be a breakthrough in attitude. We must challenge the historical standard of performance (see exhibit 1) and must prove to others that there is both a need and a way to do better.
The Juran Trilogy
Exhibit 1
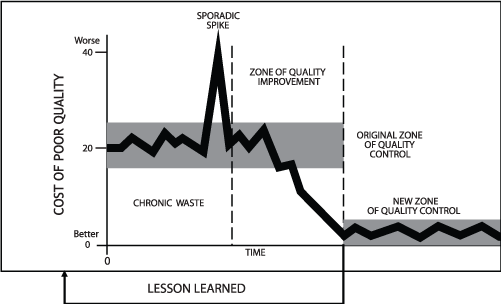
Next, there often must be a breakthrough in organization. Typically, the reasons for poor performance lie across functions and departments within an organization. Historically, no one has been responsible for solving these cross-functional problems. Therefore, we must often create new organizational forms that are responsible for (1) identifying chronic problems and (2) solving those chronic problems. The recommended way to do this would be to form a high level Quality Council that consists of senior executives to provide leadership to this effort. As a start, projects can be selected based on the cost of poor quality and cross-functional managerial teams should be selected to solve these problems.
Achieving a new level of performance also requires a breakthrough in knowledge. We must reach new plateaus in our knowledge of how the process operates and what causes poor performance. But this new knowledge alone is often not sufficient to guarantee that a new level of performance will be attained. It should be noted that people work in the process and are accustomed to the historical level of performance. Hence, we must also achieve a breakthrough in cultural patterns. This involves such things as dealing with cultural resistance to change and provide training in the new methods. Finally, we must implement the new methods and verify a breakthrough in results. Quality improvement and substantial breakthroughs in performance will not occur unless all these contributing breakthroughs are achieved. A graphic representation is shown in exhibit 2.
The Breakthrough Cycle
Exhibit 2
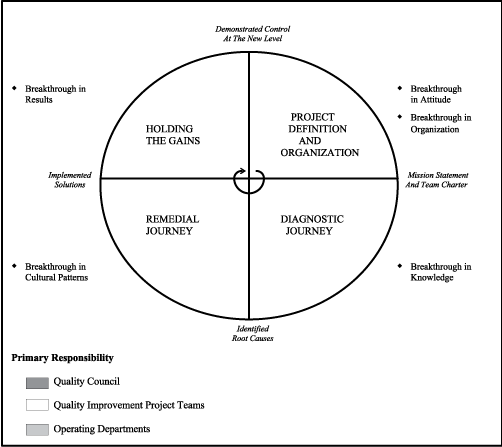
A few companies in India are using this approach to quality improvement and have seen success. The reduction in cost of poor quality in these companies is substantial and the savings have run into several lakhs of rupees per annum. There is considerable evidence to suggest that the cost of poor quality in any organization, in India, is around 20% of sales revenue. By implementing a quality improvement programme, companies are bound to improve quality and reduce such quality related costs. On the other hand, there is very little evidence to suggest that substantial reductions in cost can be achieved merely through ISO 9000.
Customer Satisfaction
Even if an organization were to eliminate all deficiencies in its existing products, services and processes, does it guarantee customer satisfaction? Maybe, maybe not. It will depend on whether products and services are designed to meet customer needs. To get more customer-driven, companies need to adopt modern quality planning methods to plan their processes and products. This will require abandoning the traditional approach to quality planning. It will require companies to adopt a structured systematic approach to quality planning to benchmark and be Best-in-Class. The structured systematic approach to Quality Planning is shown in exhibit 3.
The Quality Planning Roadmap
Exhibit 3
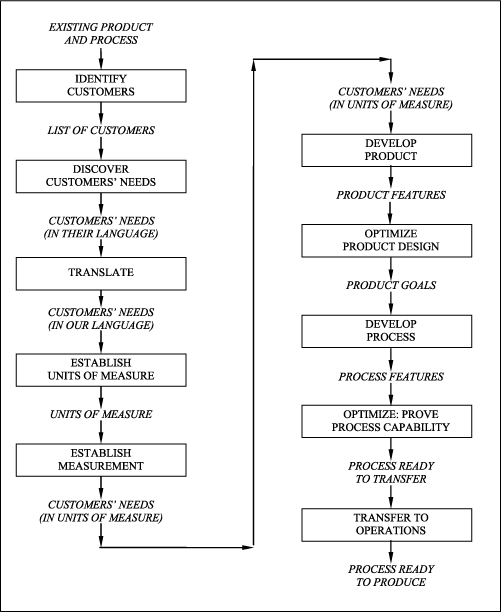
By the use of such an approach, customers would get what they want and not have to choose from what is available. It will lead to greater customer satisfaction and hence increased market share of companies, making their products more saleable worldwide.
Conclusion
Although the ISO 9000 lays a sound foundation to a total quality system, as a stand alone it is not enough. In fact, hardly adequate. To achieve quality leadership requires that companies be customer driven and make a habit of annual improvements. Companies that wish to lead the quality race must set upon themselves stretch goals, such as, to reduce the cost of poor quality by 50 per cent and simultaneously be certified as Best-in-Class by over 50 per cent of its customers by 1992.
CREDITS: Suresh Lulla, Founder & Mentor, Qimpro Consultants Pvt. Ltd.